
New Viwinco Glass Facility Update for June
After over a year of construction, the new Viwinco state-of-the-art glass facility is nearing completion. The new building will contain the entire IGU processing operation for the company, and will house entirely new machinery aside from an existing Erdman IGU line in the main facility. Meticulously planned out by Viwinco’s Engineering Department and upper management, the new glass facility was designed from the start with Lean manufacturing principles in mind to capitalize on the capabilities of the modern machinery. Once completed, the glass facility will consist of: four glass cutting tables, one tempering furnace, one laminating line, one PVB cutter, two glass seamers, four Erdman IGU lines and two grid processing stations. The machinery being installed in the new building includes the industry’s most innovative technology that will drive an increase in volume, quality and consistency to support our customer’s growth with the products they come to rely on.
New Glass Machinery
Bürkle Easy-Lam IFL — Laminating Line
The Bürkle Easy-Lam IFL laminating line will entirely revolutionize the way we manufacture our impact glass and will significantly reduce the cycle time per glass unit. Traditionally, the laminated glass is run through a thermal oven where the PVB is fused with the glass lites. It is then subjected to a lengthy heat and pressure cycle in the autoclave. Not only does this create a bottleneck in production, but if glass needs to be remade, the turnaround time for that unit can be lengthy. The Bürkle line does away with the traditional autoclave process in favor of three heavy presses to produce the laminated lites. The first press is a heated vacuum press to remove the air from between the different layers. The second press applies heat and pressure required to create the laminated glass. The final step is a cooling press to remove the heat and apply safe handling as the units are removed from the line. In total, the cycle time is approximately 12-minutes, a significant improvement over the previous cycle time in the autoclave of over 3-hours. Along with the impressive machinery comes intelligent software to assist with glass alignment and yield operation. The Bürkle line will be monumental as we continue to support impact product growth in the southern and coastal areas.

Glaston FC Series Tempering Furnace
The Glaston FC Series tempering furnace combines the next generation of tempering machinery with highly sophisticated software to manage the production of tempered glass lites. A historically complex process, glass tempering is a highly variable process that includes formulas that will change by glass batch. The furnace’s intelligent software provides enhanced control over the tempering process to ensure accuracy with the tempering formulas. The furnace also includes Active Edge Control to minimize edge lift as the heated glass moves along the rollers. The Glaston furnace will ensure high-quality tempered glass is consistently being produced.

Eastman PVB Cutter
The Eastman PVB Cutter will be used to cut our Polyvinyl Butyral (PVB) laminate glass interlayer. Having conducted initial tests on the Eastman cutter, not only is the cutter impressively fast, but it is also highly accurate. The cutter is capable of producing cuts in almost any shape at variable sizes with little to no scrap.
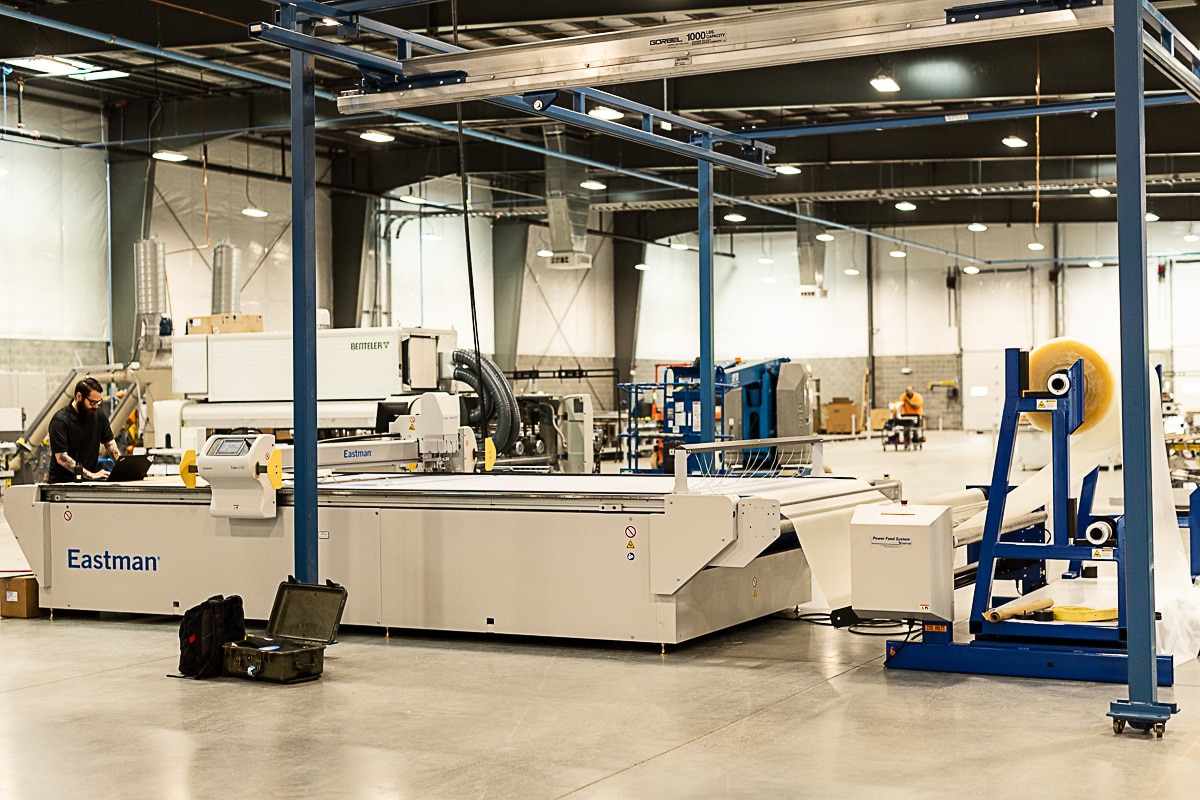

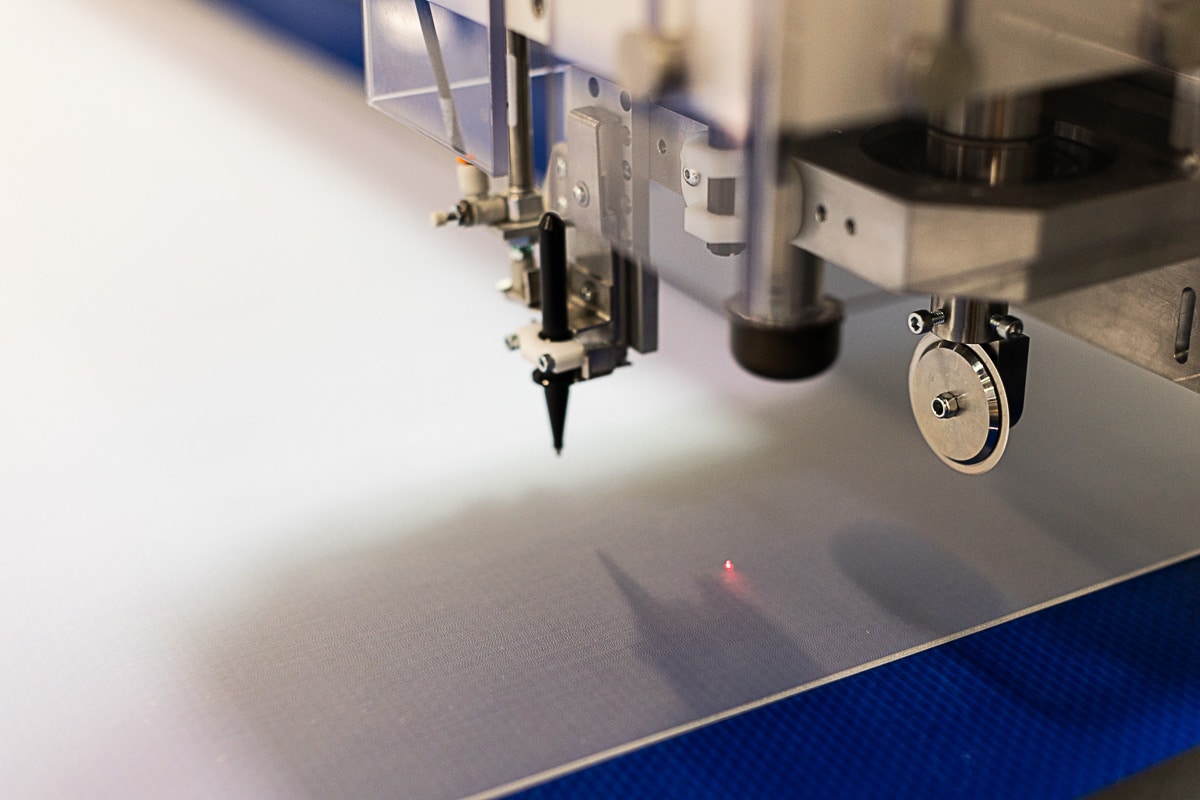
Billco Ultra Series — Glass Cutter
The Billco Ultra Series glass cutter is an impressively accurate glass cutting table designed for high-volume manufacturers. These tables are built for shorter cycle times, better glass yields and less operator intervention. In addition to the cutter tables, we also have automated unstackers that run along tracks to bring the next glass sheet to the cutting table. This will reduce the frequency in which a material handler will need to change out the glass racks and reduce idle time at the glass cutter table. The new glass facility will contain four of these glass tables.


Erdman High-Speed Dura IG Lines
We have purchased three new Erdman IG lines and will be transferring an existing Erdman line from our main facility into the new glass facility to handle the IGU assembly. The Erdman lines are highly sophisticated and significantly improve IGU assembly compared to the traditionally manual process. The line consists of multiple modules necessary to produce an IGU which include: a washing station, spacer applicator, grid station, thermal corner weld, argon station and a fourth corner seal. The Erdman lines are highly automated and can consistently produce a high-quality product. This allows us to reallocate our line workers to other areas of production where they are needed. The four Erdman lines will assist in reducing IGU production time and significantly increase the glass facility’s capacity.

Benteler Glass Seamers
The new Glass Facility will include two new glass seamers by Benteler, one of which will be fed directly into the tempering furnace. This seamer will configure the glass prior to entering the furnace to ensure the correct placement. The glass will then be automatically fed into the glass furnace without the need for operator intervention. Traditionally this was a manual process that created wasteful time for an already time-consuming process.


Grid Stations
We have also purchased two grid machines to handle the production of our flat and deluxe contoured grids. These grid stations will expedite the grid process and ensure consistent quality.

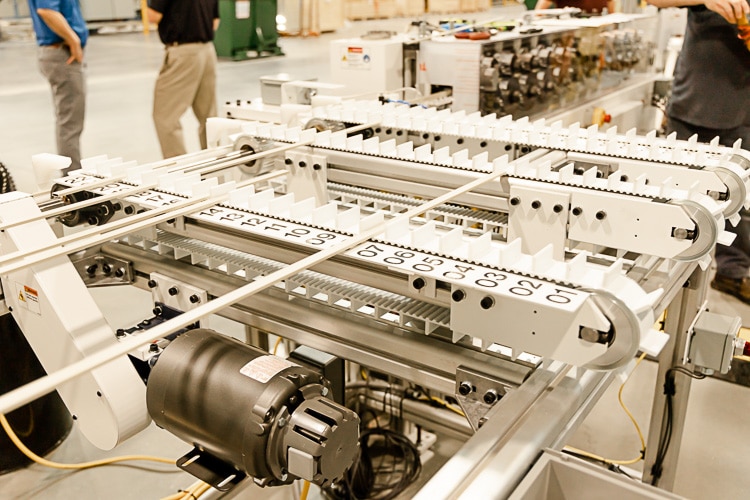
Next Steps for the Glass Facility
With most of the machinery fully installed, and electricity powering the building, the focus is now being shifted to completing the necessary qualification tests to ensure the machinery is configured appropriately. Since the new machinery is significantly different than the existing glass equipment, we will also need to begin training employees on the latest equipment and process flow within the glass facility and the transfer of materials into the main facility. Though a lot of progress has been made, there is still considerable work to be done before the glass facility is fully operational. We will continue to provide progress updates and will assign a completion date as it is made available.